Much of today’s oil and gas infrastructure is expected to continue operating into the foreseeable future, despite having exceeded its original design life. In-line inspection solutions are imperative to ensure that assets are operated as safely, efficiently, and economically as possible. It’s important to keep in mind the multiple factors that can affect how well an ILI performs, as well as the general type of tools currently available.
Prior Assessments – Piggability & Factory Assessment Testing
Before the in-line inspection, a piggability assessment should be conducted to determine whether the pipeline is safe for in-line tools. A pipeline must be in a clean condition before an In-line Inspection (ILI) run – loose or adhered deposits and scale can cause a range of issues, resulting in the tool sensors being damaged, loss of data, and even for the tool to get stuck in the pipeline. The ILI tools themselves must also meet the specifications of the site once they’ve been mobilised, to give confidence that the end-users will not be disrupted in subsequent tool runs. Whilst ILI technology has developed and improved over the years, there can still be anomalies in the data, and product flows can still be halted – assessment on tool sustainability and logistics will help create a successful strategy and basis of recommendation on inspection technology.
Intelligent/Smart Inspection Tools
Different ILI tools have been developed over the years to help manage specific integrity threats. The general classifications for the tools are:
- Geometry detection tools – A tool that utilises inertia to measure the bore of the pipe, to identify pipeline movement
- Calliper tools – to detect variation in the inside surface of the pipe such as ovality or dents
- Metal loss detection tools – Magnetic Flux Leakage (MFL) and Ultrasonic are two common metal loss detection methods, with MFL being the most commonly used in ILI technology. Magnetic Flux Leakage (MFL) provides an indirect measurement of metal loss, and with additional sensors discriminates between internal and external defects
- Crack detection tools – Ultrasonic shear waves and EMAT (Electro-Magnetic Acoustic Transducer) are used in detecting crack-like features
Speed control is also available for the type of tool implemented, giving the pipeline operators flexibility in throughput, resulting in optimal data acquisition.
Tool Feasibility
The selection of the appropriate ILI tools should be a result of a review that identifies how susceptible a pipeline is to a threat. To get the best results from an inspection, the review of the threats, the specification of the pipeline, and the tools expected performance must be considered. Each ILI tool type has its advantages and disadvantages, so understanding and implementing the correct tool, or even a combination of tools (combo-tools) can help avoid a pipeline failure.
Reporting
Documentation is a key part of any inspection activity. Documentation will be required that records the completion of inspection activities safely and successfully, including operational procedures, project method statements, lifting plans, HAZID reviews, and health and safety assessments. A Final Report should summarise the important operational information (i.e. run preparation, running of the tool, etc) and provide information on the success of the inspection and quality of data collected. In all situations, the primary objective should be to maintain safety. Secondary considerations, e.g. pipeline criticality, should then be used to determine the maximum allowable time before on-site investigation shall take place.
Successful, in-depth reporting functions as part of good communication & co-operation between the ILI service provider and the pipeline operator is a key element of successful ILI inspections. Understanding the causes of failed ILI runs is key to improving first run success rates, and to understanding the responsibility for run failure and requirements for cost recovery.
Questions? Contact usRelated Insights
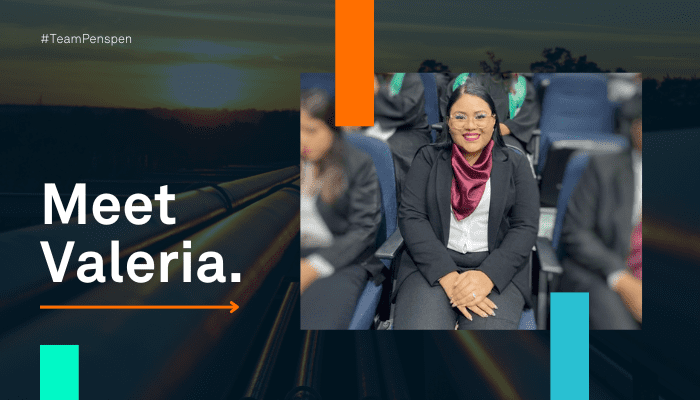
“My disability does not define my capacity.” Our People – Valeria
For several years, Penspen has been a proud supporter of Youth Building the Future, a program established by the Government of Mexico’s Ministry of Labor and Social Security to offer young people...
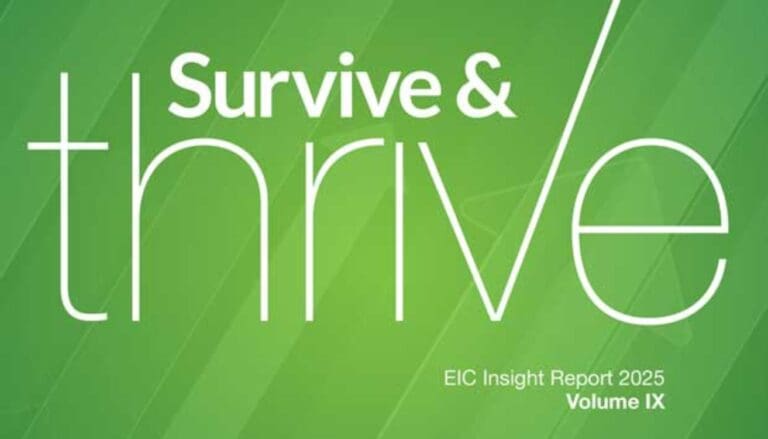
EIC Survive & Thrive Report 2025
The Energy Industries Council (EIC), the UK’s leading trade association for the energy supply chain, has published its 2025 Survive & Thrive Report. As one of 135 member companies featured and...
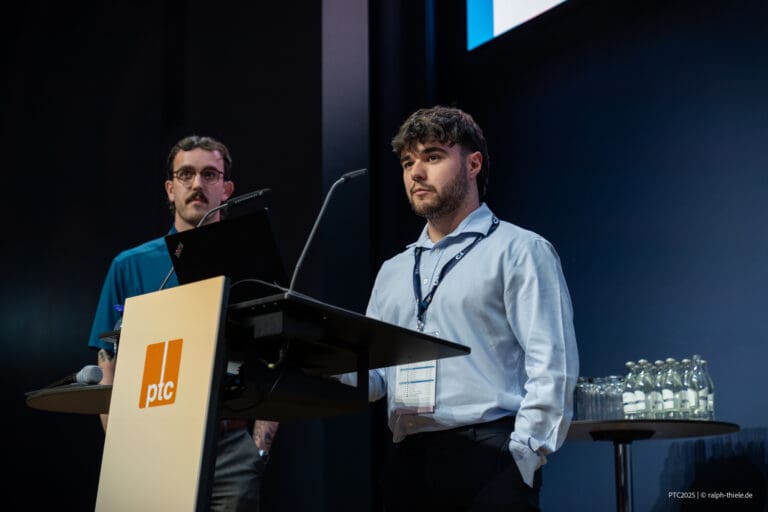
Challenges and Considerations for Hydrogen Integration in Natural Gas Pipeline Networks: A Comparative Screening Methodology
The global transition to hydrogen is accelerating, and repurposing existing natural gas pipelines is a critical step towards a low-carbon future. However, ensuring the feasibility, safety, and...
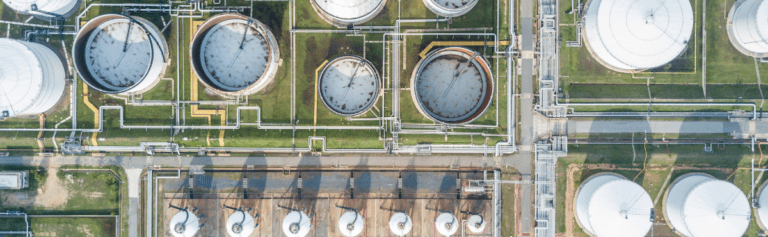
Overcoming the Challenges in Implementing a Risk-Based Inspection (RBI) Program
Risk Based Inspection (RBI) is a risk assessment and management process that focuses on loss of containment of pressurised equipment in processing and refining facilities, due to applicable damage...