Risk-Based Inspection (RBI) is a systematic tool for managing risk by prioritising equipment for inspection activities. RBI is a sound and proven asset integrity methodology and an excellent tool for prioritising and optimising inspection activities, identifying and understanding risk drivers, and creating effective risk mitigation strategies.
Risk-Based Inspection Evolution
Risk-Based Inspection has evolved, in the early days, inspection programs were designed as Run-to-Failure (RTF) in which assets are used until they break down or they require repair or replacement. This strategy was not favourable as it would result in safety incidents, unplanned production outages, and negative financial impact. Inspection teams started developing a philosophy to inspect based on some percentage of equipment life (such as 1/2 life). But even this strategy remained uneconomical since several assets failed between the half-lives. As a result, inspection experts began to think outside the box which led to establishing intervals or due dates between inspections. With the need to periodically verify equipment integrity, organisations initially resorted to time-based or “calendar-based” intervals or due dates.
However, the problem was not yet solved, as managing inspections remained costly. In the meantime, The American Petroleum Institute (API) came into action. According to API consideration, it was anticipated that with advances in inspection approaches, and better understanding of the type and rate of deterioration, inspection intervals or due dates became more dependent on the equipment condition (i.e., condition-based inspection), rather than what might have been an arbitrary date. Codes and standards such as API 510, API 570, and API 653 evolved during this time.
Inspection Program Effectiveness
The effectiveness of inspection programs varies widely, ranging from reactive to proactive programs; one extreme of this would be the “Run-to-Failure” approach while the other would be a complete inspection of all equipment items frequently. To manage these two extremes, the next generation of inspection approach and interval setting methodology evolved, where the ultimate goal is the safety and reliability of facilities. RBI is a risk-based approach that focuses specifically on loss of containment of pressurised equipment in process facilities due to material deterioration. The risk is managed primarily through equipment inspection to as low as reasonably practical (ALARP). Risk-based inspection is a sound and proven asset integrity methodology and an excellent tool for prioritising and optimising inspection activities, identifying, and understanding risk drivers, and creating effective risk mitigation strategies.
For more information on how we can support you in developing a Risk Based Inspection program, get in touch with one of our asset integrity experts below.
Contact UsRelated Insights
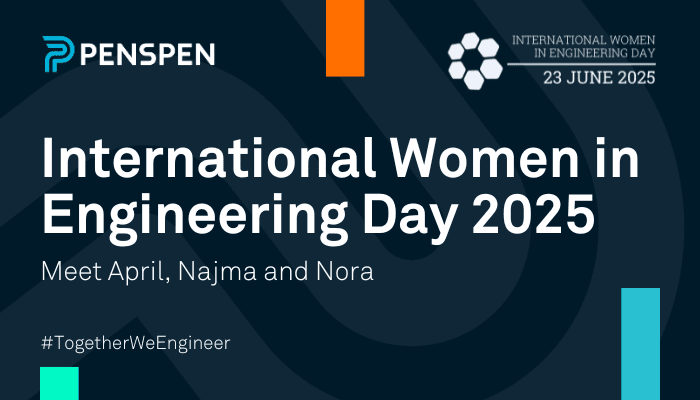
International Women in Engineering Day: Meet April, Najma and Nora
In this second edition, meet April, As-Build Coordinator & Lead CAD Associate at C&I Engineering, a company acquired by Penspen in 2024; Najma, Senior Finance Officer based in Abu Dhabi; and Nora,...

International Women in Engineering Day: Meet Shobhina, Maria and Rachael
The energy industry is changing rapidly, and meeting the challenges posed by this transition requires a diversity of talent and perspectives – something that we’re committed to addressing in a...
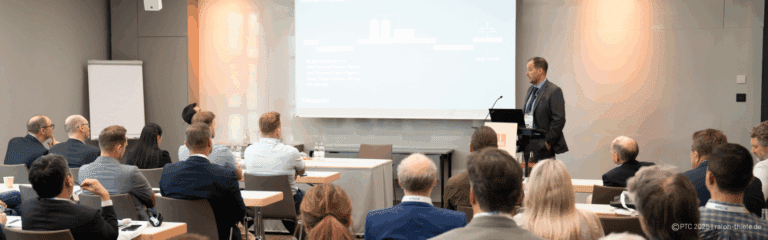
Carbon Capture, Utilisation and Storage – What are the Real Challenges & Costs?
As the global push for net zero intensifies, Carbon Capture, Utilisation, and Storage (CCUS) is emerging as a critical technology to decarbonise energy supplies and industrial processes. With the...
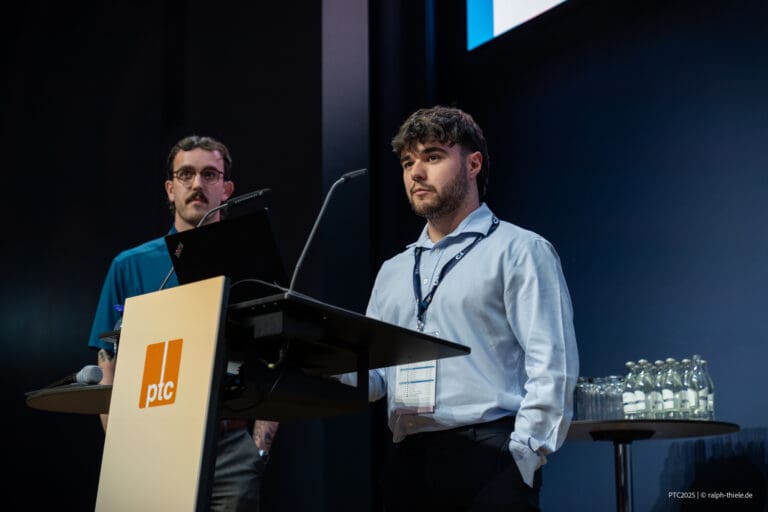
Challenges and Considerations for Hydrogen Integration in Natural Gas Pipeline Networks: A Comparative Screening Methodology
The global transition to hydrogen is accelerating, and repurposing existing natural gas pipelines is a critical step towards a low-carbon future. However, ensuring the feasibility, safety, and...